Įvadas
Anglies pluošto vamzdžiai, pagaminti pultuojant tapo pagrindine konstrukcine medžiaga įvairiose pramonės šakose dėl savo puikus tvirtumo ir svorio santykis, išskirtinės medžiagos savybės, ir atsparumas korozijai. Šie vamzdžiai plačiai naudojami aviacijos, automobilių, statybos, sporto įrangos ir pramonės srityse, kur didelis stiprumas (anglies pluošto vamzdžio stiprumas) ir ilgaamžiškumas yra labai svarbūs.
Svetainė anglies pluošto vamzdžių gamybos procesas vaidina lemiamą vaidmenį nustatant galutinio gaminio eksploatacines savybes, stiprumą ir kainą. Tarp įvairių gamybos metodų, gijų vyniojimas ir pultrusija yra du dažniausiai naudojami metodai, skirti įvairių tipų anglies pluošto vamzdžiai (anglies pluošto vamzdžių atsargos), įskaitant preprego anglies pluošto vamzdžiai, anglies pluošto kvadratiniai vamzdžiai, ir pultruduoti anglies pluošto vamzdžiai.
Šiame straipsnyje išnagrinėsime šių dviejų procesų skirtumus ir padėsime jums pasirinkti geriausią gamybos būdą pagal medžiagos savybės, anglies pluošto vamzdžio kaina, anglies pluošto vamzdžio stiprumas ir gamybos efektyvumas.
Kas yra anglies pluošto vamzdžiai?
Anglies pluošto vamzdžiai, pagaminti pultuojant yra tuščiavidurės cilindrinės konstrukcijos, pagamintos iš anglies pluošto medžiagos (anglies pluošto rankovė) kartu su dervos matrica. Šie vamzdžiai siūlo didelis stiprumas, mažas svoris ir puikus patvarumastodėl jie idealiai tinka konstrukcinėms ir mechaninėms reikmėms.
Veikimas anglies pluošto vamzdžiai labai priklauso nuo gamybos metodo ir anglies pluošto vamzdžių pelėsių naudojamas gamybos metu. Be to, anglies pluošto vamzdžio kaina priklauso nuo formos sudėtingumo, gamybos metodo ir medžiagos kokybės.
Anglies pluošto vamzdžių gamybos procesai
1. Gijų vyniojimo procesas
Kas yra gijų vyniojimas?
Gijų vyniojimas yra gamybos procesas, kurio metu ištisinės anglies pluošto gijos (anglies pluošto įvorė) impregnuojami derva ir tam tikru kampu vyniojami aplink besisukantį įtvarą. Šis metodas leidžia gamintojams kontroliuoti pluošto orientaciją, maksimaliai padidinant anglies pluošto vamzdžio stiprumas norimomis kryptimis.
Šis procesas idealiai tinka didelio skersmens, didelio stiprumo anglies pluošto vamzdžiams arba individualiems konstrukciniams komponentams, pvz. preprego anglies pluošto vamzdžiai arba didelis anglies pluošto slėginiai indai.
Gijų vyniojimo privalumai
- ✅ Pritaikoma pluošto orientacija: Gijų vyniojimas leidžia gamintojams reguliuoti vyniojimo kampą ir taip optimizuoti medžiagos savybės (Anglies pluošto vamzdžių savybės) maksimaliam stiprumui tam tikra kryptimi užtikrinti.
- ✅ Didelis stiprumas ir ilgaamžiškumas: Anglies pluošto vamzdeliai, pagaminti vyniojant gijas, pasižymi geresnėmis savybėmis atsparumas sukimui, atsparumas lenkimui, ir atsparumas ašinei apkrovai.
- ✅ Sudėtingos geometrijos: Šis metodas tinka dideliems, sudėtingos formos anglies pluošto vamzdžiams, įskaitant anglies pluošto kvadratiniai vamzdžiai arba kitų pasirinktinių skerspjūvio formų.
Paraiškos
- Aviacijos ir kosmoso konstrukciniai komponentai
- Pramoniniai robotai, mechaninės rankos
- Aukšto slėgio indai, laikymo talpyklos
2. Pultruzijos procesas
Kas yra pultrusija?
Pultrusion tai nepertraukiamas ir automatizuotas anglies pluošto vamzdžių gamybos procesas, kurio metu ištisiniai anglies pluošto ryšuliai (anglies pluošto rankovė) traukiami per dervos vonia ir po to per įkaitintą formą. Formoje formuojamas vamzdis, o šiluma kietina dervą, todėl gaunamas nuoseklus ir vienodas skerspjūvio profilis.
Šis procesas idealiai tinka didelės apimties gamybai anglies pluošto vamzdžiai, ypač anglies pluošto kvadratiniai vamzdžiai arba pultruduoti anglies pluošto vamzdžiaikai reikia didelio tikslumo ir mažų sąnaudų.
Pultruzijos privalumai
- ✅ Didelės apimties gamyba: Pultruzija yra visiškai automatizuotas procesas, todėl labai tinka masinei gamybai. anglies pluošto vamzdžių atsargos pastovios kokybės.
- ✅ Nuoseklūs skerspjūvio profiliai: Šis procesas užtikrina, kad visi anglies pluošto vamzdžiai yra vienodo skersmens, storio ir formos, todėl idealiai tinka standartiniams konstrukciniams komponentams.
- ✅ Žemesnė anglies pluošto vamzdžių kaina: Pultruzija gerokai sumažina gamybos sąnaudas, nes ji yra labai automatizuota, todėl idealiai tinka ekonomiškai efektyviai didelio masto gamybai.
- ✅ Didelis atsparumas tempimui: Pultruduoti anglies pluošto vamzdžiai pasižymi puikiomis atsparumas tempimuiatsparumas smūgiams ir pastovios medžiagos savybės.
Paraiškos
- Pramonės mašinų konstrukciniai atraminiai strypai
- Automobilių dalys ir komponentai
- Statybos ir infrastruktūros taikymai
- Sporto įranga, pavyzdžiui, meškerės ir golfo lazdos.
Gijų vyniojimas, palyginti su gijų išspaudimu: Pagrindiniai skirtumai
Palyginimo kriterijai | Gijų vyniojimas | Pultrusion |
---|---|---|
Pluošto orientacija | Reguliuojamas; optimizuotas kryptiniam stiprumui | Fiksuotas išilgai vamzdžio ašies |
Sudėtingos geometrijos | Gali sukurti sudėtingas formas, pvz. anglies pluošto kvadratiniai vamzdžiai | Palaiko tik vienodus skerspjūvio profilius |
Gamybos greitis | Lėta, daug darbo jėgos reikalaujanti gamyba | Greita, nepertraukiama gamyba |
Gamybos sąnaudos | Didesnis dėl darbo jėgos ir medžiagų švaistymo | Mažiau dėl automatizuotos masinės gamybos |
Paraiška | Didelio atsparumo, pagal užsakymą suformuoti anglies pluošto vamzdžiai | Masinės gamybos anglies pluošto vamzdžių atsargos |
Kaip pasirinkti geriausią gamybos procesą
1. Remiantis medžiagos savybėmis
Jei jūsų produktui reikia didelis atsparumas tempimui ir specifinis krypties stiprumas, pavyzdžiui, orlaivių dalys arba slėginiai indai, gijų vyniojimas yra geriausias pasirinkimas. Šis procesas leidžia gamintojams kontroliuoti pluošto orientacija ir optimizuoti vamzdžio stiprumą norimomis kryptimis.
Tačiau, jei jums reikia vienodas vamzdžio stiprumas (Anglies pluošto vamzdžių savybės). su minimaliu pritaikymu, pultrusija siūlo geresnį sprendimą masinei gamybai.
2. Remiantis anglies pluošto vamzdžio kaina
- Gijų vyniojimas reikalauja didesnių darbo sąnaudų, brangių formų ir sudėtingų procesų, todėl anglies pluošto vamzdžio kaina santykinai didelis.
- Pultrusion yra visiškai automatizuotas procesas, kurio metu mažesnė anglies pluošto vamzdžio kainatodėl jis idealiai tinka didelės apimties gamybai.
3. Remiantis anglies pluošto vamzdžių forma
Sudėtingumas anglies pluošto vamzdžių pelėsių taip pat turi įtakos gamybos sąnaudoms.
- Svetainėje gijų vyniojimas, kiekvienai nestandartinei formai reikia naujos formos, o tai didina gamybos sąnaudas.
- Svetainėje pultrusija, viena forma galima pagaminti tūkstančius vienodų anglies pluošto vamzdelių, todėl gerokai sumažėja formos sąnaudos.
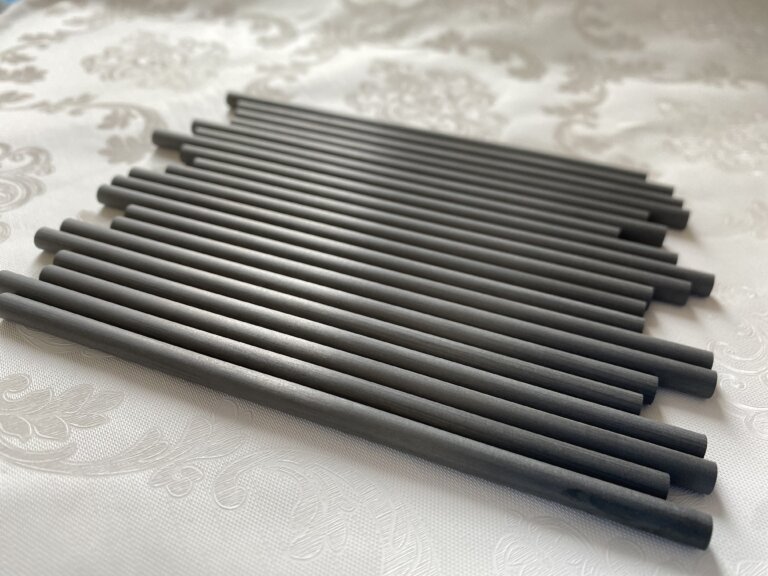
Išvada
Pasirinkti tinkamą anglies pluošto vamzdžių gamybos procesas priklauso nuo jūsų gaminio konstrukcijos, reikiamų medžiagų savybių ir gamybos apimties.
- ✅ Jei reikia didelio stiprumo, pritaikyti anglies pluošto vamzdžiai (anglies pluošto vamzdžių stiprumas), gijų vyniojimas yra geriausias pasirinkimas.
- ✅ Jei reikia didelio masto gamyba su mažu anglies pluošto vamzdžio kaina, pultrusija yra ekonomiškesnis.
Svetainėje "CarbonCore Dynamics, mes specializuojamės gamyboje aukštos kokybės anglies pluošto vamzdžiai, įskaitant anglies pluošto kvadratiniai vamzdžiai, pultruduoti anglies pluošto vamzdžiai, ir pagal užsakymą CNC anglies pluošto dalys. Nesvarbu, ar jums reikia pritaikyti didelio stiprumo anglies pluošto vamzdžiai ar didelės apimties gamybai, siūlome sprendimus, atitinkančius jūsų biudžeto ir našumo reikalavimus.
👉 Susisiekite su mumis šiandien sužinoti daugiau apie mūsų anglies pluošto vamzdžių atsargos, gamybos pajėgumus ir konkurencingumą anglies pluošto vamzdžių kainos.
Nuorodos:
1.Tinkamo anglies pluošto vamzdelio pasirinkimas jūsų meškerykočiui
2.Iš ko galima pagaminti anglies pluošto vamzdžius?
3.Anglies pluošto vamzdžių galios atskleidimas: Lengvų ir lanksčių teleskopinių vamzdžių ateitis
4.Anglies pluošto vamzdžių kietumo ir suspaudimo bandymų supratimas
5.Kaip pasirinkti tinkamus anglies pluošto vamzdžius savo projektui
6 atsakymai