Rohre aus Kohlefaser werden immer mehr zu unverzichtbaren Komponenten in einer Vielzahl von Branchen, von der Luft- und Raumfahrt bis zur Automobilindustrie. Diese leichten und doch unglaublich starken Materialien bieten eine bemerkenswerte Kombination aus Stärke, Haltbarkeit und Vielseitigkeit. Bevor jedoch ein Produkt für die vorgesehene Anwendung eingesetzt werden kann, muss seine Leistung unter verschiedenen Bedingungen getestet werden. Zwei wichtige Tests sind dabei die Härte- und die Druckprüfung. Im Folgenden werden die verschiedenen Techniken und Werkzeuge, die bei diesen Prüfungen zum Einsatz kommen, näher erläutert, damit die Kunden besser verstehen, wie diese Verfahren funktionieren und warum sie wichtig sind.
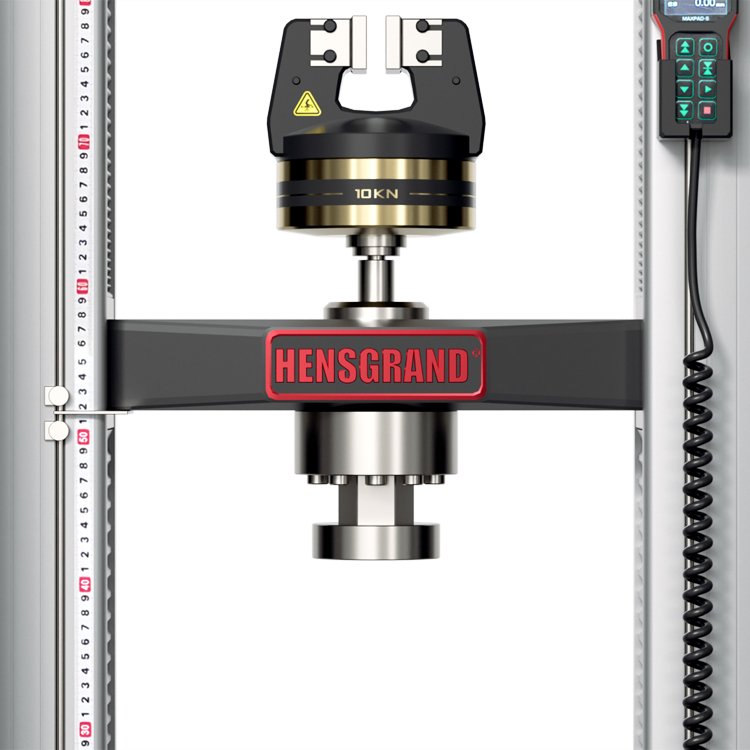
Die Bedeutung der Härteprüfung
Die Härteprüfung spielt eine entscheidende Rolle bei der Bewertung der Haltbarkeit und Verschleißfestigkeit von Kohlefaserrohre. Es ist eine Methode, mit der festgestellt wird, wie gut ein Material Kratzern, Eindrücken oder Abrieb widerstehen kann. Für die Kunden ist dies von entscheidender Bedeutung, insbesondere wenn ihre Kohlefaserrohre in Umgebungen eingesetzt werden, in denen die Oberflächenabnutzung die Gesamtintegrität beeinträchtigen könnte.
Bei der Härteprüfung wird in der Regel ein bestimmter Eindringkörper in die Oberfläche des Materials gedrückt. Die Tiefe oder Größe des Eindrucks gibt ein direktes Maß für die Härte. Es gibt mehrere Prüfmethoden, die sich jeweils für verschiedene Materialarten und Anwendungen eignen.
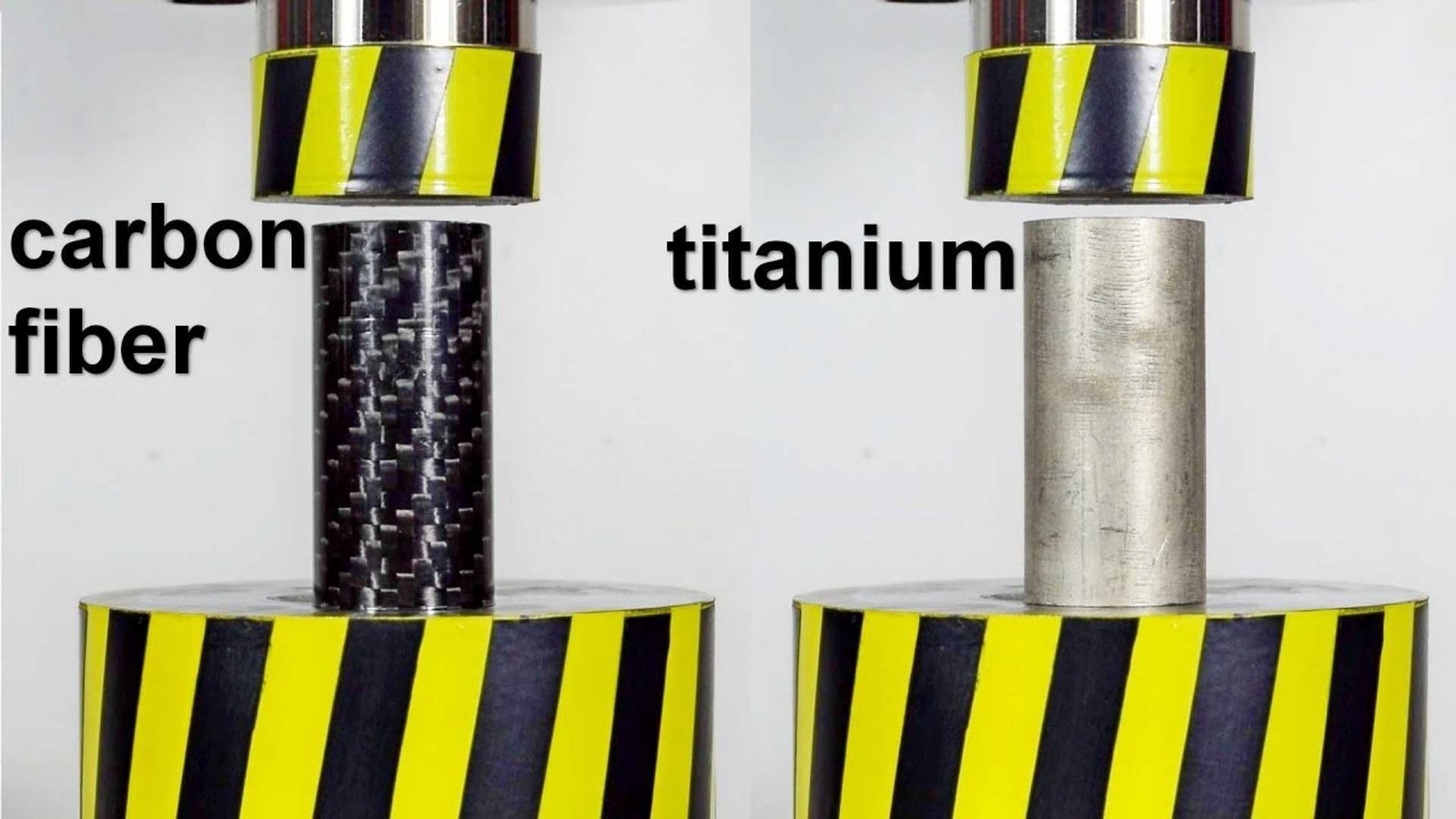
Brinell-Härteprüfung
Eines der ältesten und gebräuchlichsten Verfahren zur Härteprüfung ist der Brinell-Test. Dabei wird eine harte Stahl- oder Karbidkugel mit einem Durchmesser von typischerweise 1 bis 10 mm verwendet. Diese Kugel wird in die Oberfläche des Werkstücks gedrückt. Kohlefaserrohr unter einer bestimmten Belastung. Der Durchmesser des entstandenen Abdrucks wird dann gemessen, um die Härte zu bestimmen.
Während der Brinell-Test für Materialien wie Metalle sehr effektiv ist, stellen Rohre aus Kohlefaser eine besondere Herausforderung dar. Aufgrund der relativ geringen Oberflächenhärte des Materials im Vergleich zu Metallen kann sich der Eindringkörper manchmal verformen oder keine klaren Eindrücke erzeugen. Dennoch kann diese Technik bei bestimmten Rohrkonstruktionen aus Verbundwerkstoffen wertvolle Erkenntnisse liefern.
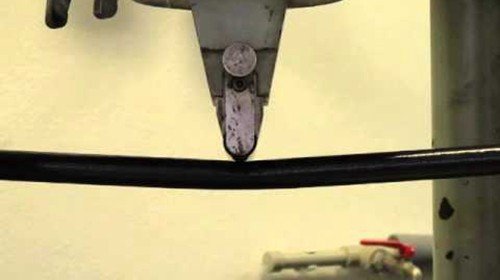
Vickers-Härteprüfung
Die Vickers-Methode ist zwar anspruchsvoller, wird aber häufig für Materialien mit harter Oberfläche verwendet. Dabei wird ein pyramidenförmiger Diamanteindringkörper verwendet, und der ausgeübte Druck ist viel größer als bei der Brinell-Prüfung. Die Vickers-Prüfung kann besonders nützlich sein für Kohlefaserrohre mit komplexen Harz- und Faserschichten, die präzisere und konsistentere Ergebnisse als der Brinell-Test liefern.
Für Kunden, die eine genauere Messung der Härte wünschen, kann der Vickers-Test ein klareres Bild davon vermitteln, wie gut das Kohlefaserrohr dem Verschleiß standhält, insbesondere bei Anwendungen wie Robotik oder Sportgeräten.
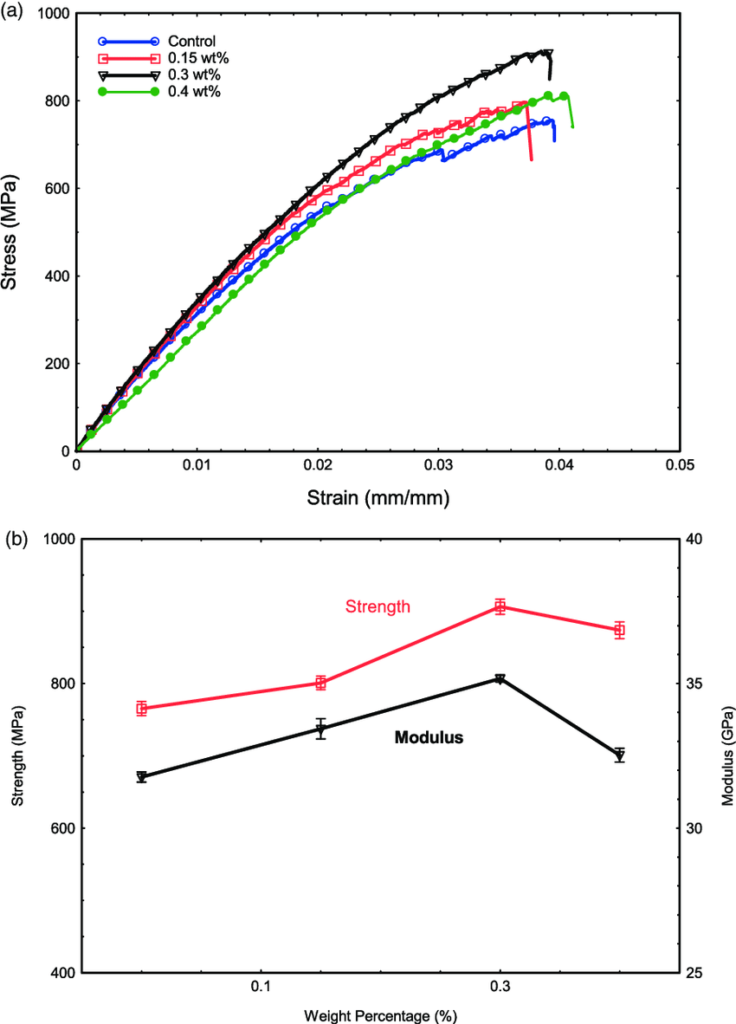
Die Rolle der Kompressionsprüfung
Während bei der Härteprüfung die Oberflächeneigenschaften bewertet werden, wird bei der Druckprüfung das Verhalten des Materials unter Belastung beurteilt. Diese Prüfung simuliert die Bedingungen Kohlefaserrohre während des Gebrauchs, insbesondere in stark beanspruchten Umgebungen, auftreten können. Für Kunden, die Kohlenstofffaserrohre für strukturelle Anwendungen wie Flugzeugteile oder schwere Maschinen verwenden, sind Druckprüfungen unerlässlich.
Ausrüstung für Kompressionsprüfungen
Druckprüfgeräte sind so konzipiert, dass sie eine kontrollierte Kraft auf das Material ausüben. Die Maschine besteht in der Regel aus zwei starren Platten, die das Prüfmuster zusammendrücken. Die Last wird schrittweise aufgebracht, bis sich das Rohr entweder verformt oder bricht.
Für KohlefaserrohreMit Hilfe dieser Tests lässt sich feststellen, wie viel Gewicht oder Druck die Rohre aushalten können, ohne dass ihre strukturelle Integrität beeinträchtigt wird. Die Kunden verlassen sich oft auf diese Ergebnisse, um zu beurteilen, ob das Material für ihre spezifischen Anforderungen geeignet ist.
Bei Hochleistungsrohren, wie sie in der Luft- und Raumfahrt oder in Sportgeräten verwendet werden, hilft die Druckprüfung, ihre Grenzen zu bestimmen. Die Prüfergebnisse liefern wichtige Daten darüber, wie sich das Material unter verschiedenen Kraftrichtungen verhält und wie es sich unter extremen Bedingungen verhält.
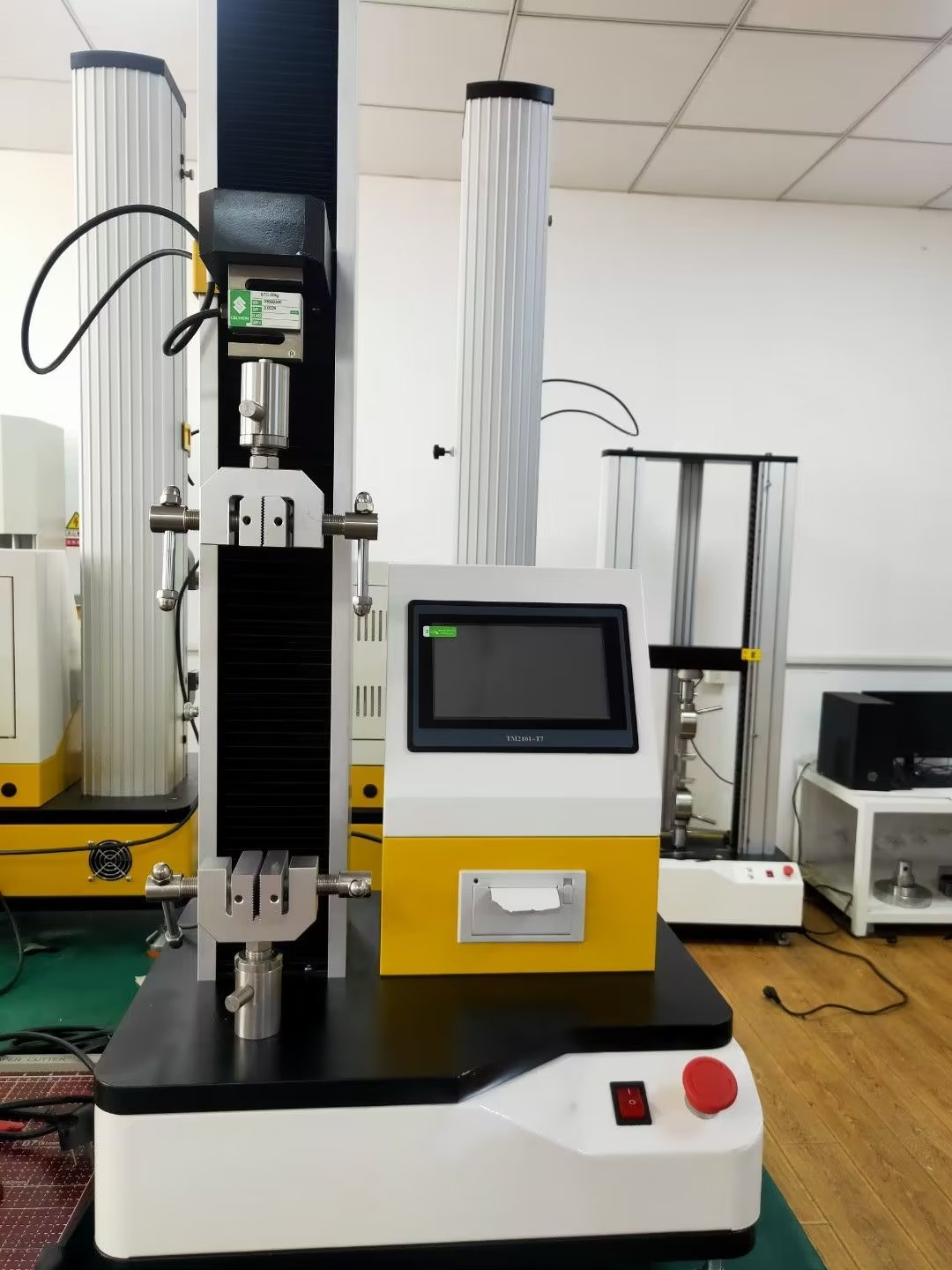
Uniaxiale Druckprüfung
Bei der einachsigen Druckprüfung, einer der am weitesten verbreiteten Methoden, wird eine Druckkraft entlang einer einzigen Achse ausgeübt. Sie ist besonders nützlich, um zu verstehen, wie sich das Rohr unter Druck in linearer Weise verhält. Kunden, die Kohlefaserrohre für strukturelle Anwendungen finden diese Methode von unschätzbarem Wert für die Bewertung ihrer Leistung unter typischen Belastungsszenarien.
In einigen Fällen kann die einachsige Druckprüfung durch fortschrittliche bildgebende Verfahren wie Röntgen- oder Ultraschallprüfungen ergänzt werden, um detailliertere Einblicke in das innere Verhalten des Materials zu erhalten. So kann die Erkennung von inneren Hohlräumen, Faserfehlstellungen oder Harzunregelmäßigkeiten kritische Schwachstellen aufdecken, die ohne fortschrittliche Diagnostik unmöglich zu erkennen wären.
Herausforderungen bei der Prüfung von Kohlenstofffaserrohren
Trotz der Vorteile von Härte- und Druckprüfungen ist die Bewertung der Leistung von Kohlefaserrohren nicht unproblematisch. Eines der Haupthindernisse ist der Verbundwerkstoffcharakter von Kohlenstofffasermaterialien. Diese Rohre bestehen oft aus verschiedenen Schichten mit unterschiedlichen Faserausrichtungen und Harzen, die die Reaktion des Materials auf Kraft beeinflussen können. Diese komplexe Struktur bedeutet, dass ein Standardtest möglicherweise kein vollständiges Verständnis des Materialverhaltens vermittelt.
Variabilität in Kohlenstofffaser-Verbundwerkstoffen
Die Art der verwendeten Kohlenstofffasern - ob gewebt, unidirektional oder als Wirrfaser - kann die Ergebnisse von Härte- und Drucktests beeinflussen. Ebenso spielt die Harzmatrix, die die Fasern miteinander verbindet, eine wichtige Rolle. So kann sich beispielsweise ein Harz mit niedriger Aushärtungstemperatur anders verhalten als ein hitzegehärtetes Harz. Dies bedeutet, dass die Kunden bei der Wahl der Prüfmethoden die Materialvariabilität berücksichtigen müssen.
Die Kunden müssen oft die richtigen Fragen stellen: Welche Art von Kohlefaserrohr ist für meine Anwendung am besten geeignet? Erfordert es spezielle Tests oder Analysen, um seine Leistung zu überprüfen? Das Verständnis für die Feinheiten des Materials hilft den Kunden bei der Auswahl der am besten geeigneten Prüfmethoden.
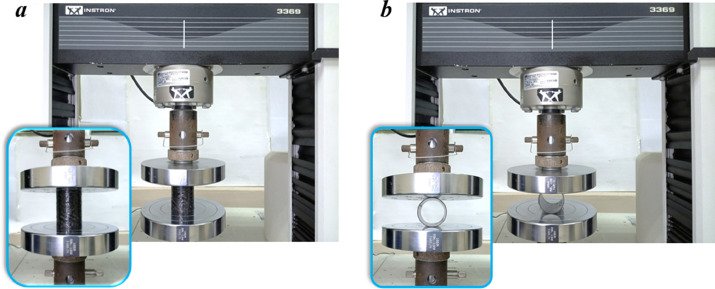
Häufige Fehler bei der Prüfung von Kohlefaserrohren zu vermeiden
Die Prüfung von Kohlefaserrohren ist zwar unerlässlich, doch können Hersteller oder Kunden bei der Durchführung des Verfahrens leicht Fehler machen. Ein häufiger Fehler besteht darin, die Tests nicht unter realen Bedingungen durchzuführen. Die Prüfung bei Standardtemperaturen und -drücken entspricht nicht immer den extremen Bedingungen, denen die Rohre in der Praxis ausgesetzt sein können.
Ein weiteres Problem liegt in der Auswahl der Prüfgeräte. Einige Kunden verlassen sich auf veraltete Geräte oder Allzweckwerkzeuge, die möglicherweise keine genauen Ergebnisse für Verbundwerkstoffe liefern. Die Wahl von Spezialwerkzeugen für Kohlefaserverbundwerkstoffe gewährleistet zuverlässigere Ergebnisse und kann auf lange Sicht Kosten sparen.
Schlussfolgerung
Härte- und Druckprüfungen sind wichtige Schritte, um sicherzustellen, dass Kohlenstofffaserrohre in anspruchsvollen Anwendungen wie erwartet funktionieren. Wenn die Kunden die verschiedenen Techniken und Instrumente kennen, können sie fundiertere Entscheidungen über die von ihnen verwendeten Materialien treffen. Ob es um die Bestimmung der Verschleißfestigkeit durch Härtetests oder die Bewertung der strukturellen Integrität unter Druck durch Drucktests geht, diese Tests bieten Erkenntnisse, die für die Auswahl des richtigen Kohlefaserrohrs für die jeweilige Aufgabe entscheidend sind.
Für Kunden bieten diese Tests eine Möglichkeit, die Leistung und Langlebigkeit von Kohlefaserrohren zu maximieren. Durch die Zusammenarbeit mit vertrauenswürdigen Testeinrichtungen und die Sicherstellung, dass die am besten geeigneten Methoden angewandt werden, können die Kunden sicher sein, dass ihre Kohlefaserrohre den harten Anforderungen des vorgesehenen Einsatzes standhalten.
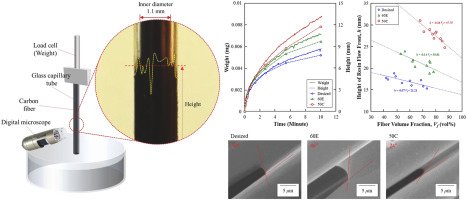
Kohlenstofffaser-Rohr Härte und Druckprüfung Bericht Probe
Produkt: Kohlefaser-Rohr
Datum der Prüfung: 2025-02-13
Muster-ID: 26*30*1000mm
Ziel des Tests: Bewertung der Härte und der Druckeigenschaften von Kohlefaserrohren, um ihre Eignung und Haltbarkeit zu überprüfen.
Sektion Kompressionstest
1. Einachsiger Druckversuch
- Testausrüstung: HY-5080 (Kompressionsprüfmaschine)
- Prüfverfahren: ASTM D695 Norm
- Muster Abmessungen: Durchmesser 20 mm, Länge 50 mm
- Belastungsrate: 1 mm/min
- Maximale Druckbelastung: 120 kN
- Kompressionsmodul: 40 GPa
- Versagenslast: 118 kN
- Frakturspannung: 400 MPa
- Maximale Verformung: 2,3 mm
2. Analyse des Kompressionsverhaltens von Verbundwerkstoffen
- Test Standard: ISO 14129
- Probenart: Gewebtes Kohlenstofffaser-Rohr
- Druckfestigkeit: 320 MPa
- Maximale Verformung: 4,2 mm
- Versagensmodus: Ausbreitung von Mikrorissen in der Rohrwand
Zusätzliche Tests
1. Rückprall-Leistungstest
- Prüfverfahren: ASTM D3410
- Elastischer Modul: 30 GPa
- Rückprallrate: 90%
2. Erkennung interner Defekte (z. B. Ultraschallprüfung)
- Prüfverfahren: Ultraschall-C-Scan
- Muster Abmessungen: Durchmesser 25 mm, Länge 100 mm
- Defekt-Typ: Keine wesentlichen Mängel
- Häufigkeit der Tests: 5 MHz
Ergebnisse Analyse
- Analyse der Härte: Die Härteprüfung nach Vickers zeigt, dass die Oberfläche der Probe eine hohe Verschleißfestigkeit aufweist, so dass sie sich für langfristig belastende Anwendungen eignet, insbesondere für hochpräzise mechanische Bauteile.
- Analyse des Kompressionstests: Das Kohlefaserrohr kann einem Druck von bis zu 120 kN standhalten und bleibt auch bei starker Belastung stabil. Es eignet sich für strukturelle Anwendungen in der Luft- und Raumfahrt und im Automobilsektor.
- Defekt-Analyse: Die Ergebnisse der Ultraschallprüfung zeigen keine signifikanten inneren Risse oder Hohlräume, was darauf hindeutet, dass die Fertigungsqualität des Kohlefaserrohrs hoch ist.
5 Antworten