How to Manufacture Carbon Fiber Parts?
The process of creating carbon fiber parts combines technical precision with innovative methods to deliver durable, lightweight, and high-performance products. Whether you’re producing custom carbon fiber car parts or crafting carbon fiber accessories for sports equipment, this guide offers practical solutions to common challenges. Let’s explore how to manufacture these components with finesse.

Understanding the Basics of Carbon Fiber
Carbon fiber is a composite material prized for its strength-to-weight ratio. It involves weaving strands of carbon atoms into a fabric, which is then combined with a resin. This blend results in a rigid, lightweight structure, ideal for various applications such as durable carbon fiber auto body panels or lightweight carbon fiber bicycle components.
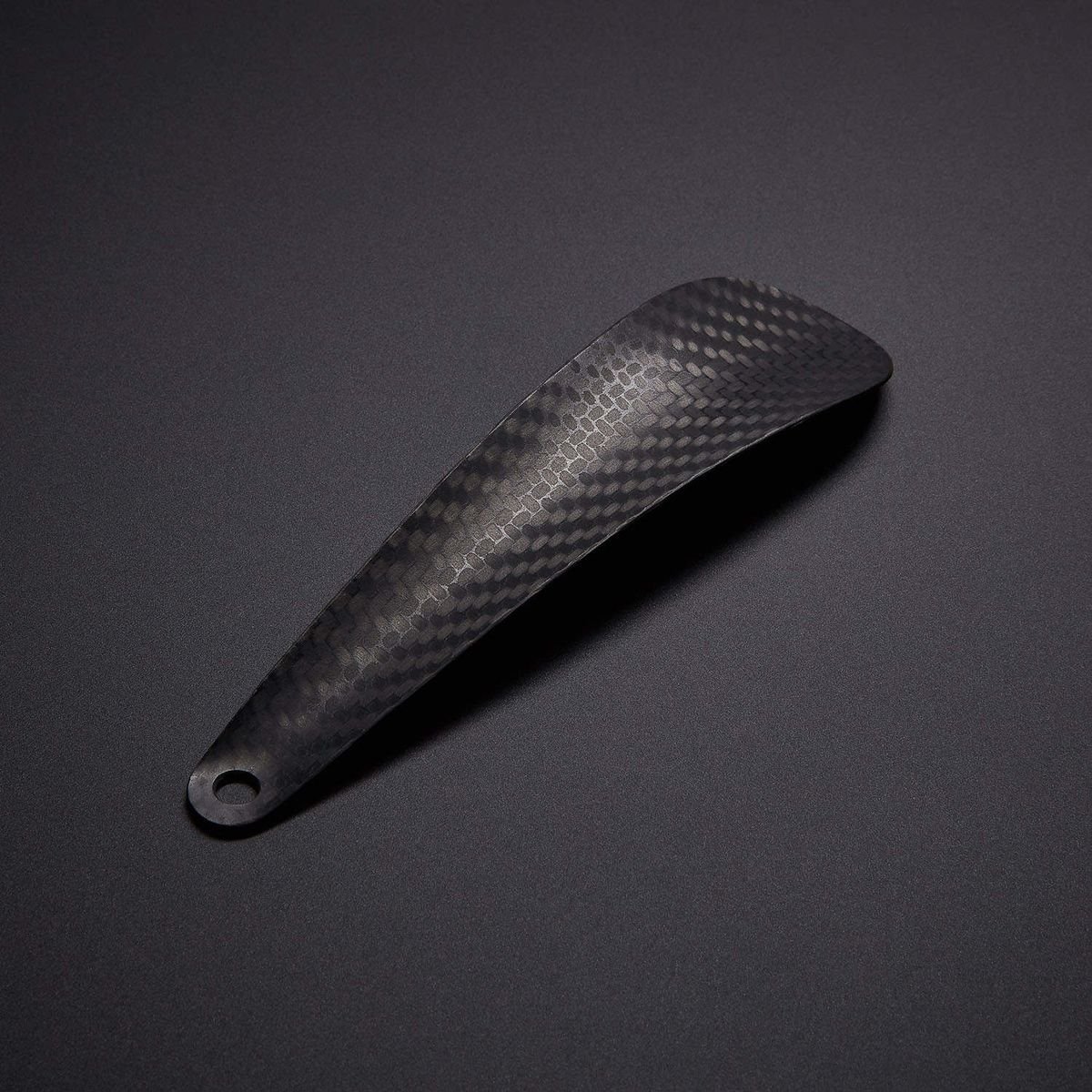
Step-by-Step Guide to Manufacturing
Designing the MoldCreating an accurate mold is the foundation of carbon fiber manufacturing. For projects like affordable carbon fiber drone frames, precision in design ensures consistent results. Use CAD software for detailed modeling, focusing on the part’s dimensions and structural requirements.
Selecting the Right MaterialChoose carbon fiber fabric that matches the intended application. High-performance carbon fiber motorcycle parts require different grades compared to carbon fiber parts for home decor. Consider factors like thickness, weave pattern, and tensile strength.
Preparing the LayupLay the carbon fiber fabric into the mold, layering it according to the design. Apply a resin matrix to bind the layers. For carbon fiber parts for racing cars, epoxy resin offers superior durability and heat resistance.
Vacuum Bagging and CuringPlace the mold in a vacuum bag to remove air pockets. This step ensures a smooth surface and uniform resin distribution. Curing the part in an autoclave or oven solidifies the structure, making it ready for use.
Trimming and FinishingAfter curing, trim excess material and polish the surface. For 3D-printed carbon fiber replacement parts, additional sanding may be necessary to refine the final appearance.

Addressing Common Challenges
Achieving Consistent QualityConsistency can be tricky, especially when producing lightweight carbon fiber bicycle components. Implementing strict quality control protocols minimizes defects.
Reducing CostsManufacturing affordable carbon fiber drone frames demands cost-effective techniques. Use automated processes like resin transfer molding to cut expenses while maintaining quality.
Environmental ConsiderationsRecycling and reusing scrap material can lower the environmental impact of producing carbon fiber parts for electric vehicles or other applications.
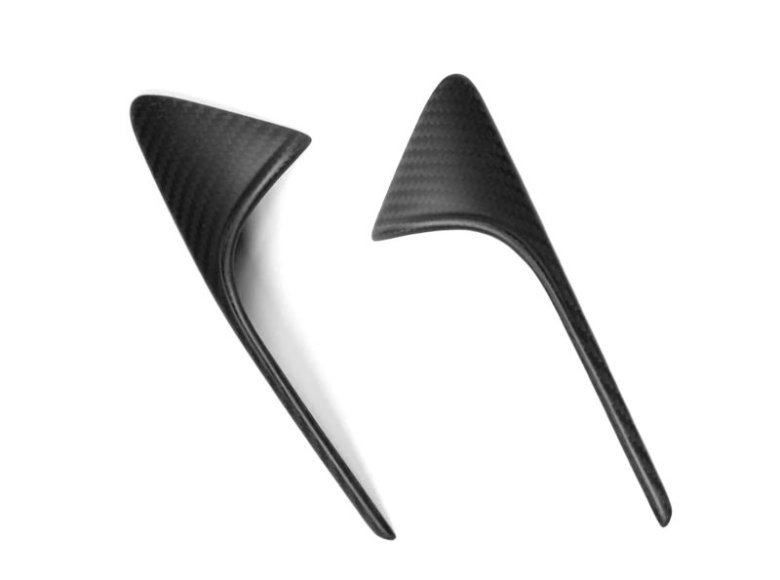
Exploring Applications
AutomotiveCustom carbon fiber car parts and durable auto body panels enhance performance and aesthetics in vehicles.
Sports EquipmentCarbon fiber accessories for sports equipment provide unparalleled strength and lightweight properties.
Home and DecorUnique carbon fiber parts for home decor merge functionality with a sleek, modern look.
Manufacturing carbon fiber parts is both an art and a science. By understanding the material, refining techniques, and addressing challenges, you can create components that meet diverse needs—from high-performance carbon fiber motorcycle parts to affordable carbon fiber drone frames. Embrace these methods to craft durable, innovative, and lightweight solutions tailored to your audience.