
Creating a simple carbon fiber tube assembly isn’t rocket science—though it sure feels close. Folks crafting telescope frames, quadcopters, or high-strength kite parts need something light yet stiff. That’s where carbon fiber tubes and connectors shine. Let’s break down how these parts come together and solve real problems for DIYers and pros alike.
Types of Carbon Fiber Connectors
Different builds ask for different joints. Connectors keep those long, lean carbon fiber tubes solid and in shape. Whether you’re building a carbon fiber telescope tube or a racing drone frame, the connection style can make or break your structure.
You’ve got:
Sleeve connectors – slide snug over two tubes
Insert connectors – push inside for a clean finish
Clamp-style joints – ideal for adjustments or temporary fits
Hybrid connectors – use clamps and inserts together
Sleeves work well for permanent frames. Inserts handle neat finishes better. Clamps, though? Lifesavers on custom rigs or field-tested setups. Need a carbon fiber tube clamp that won’t slip during vibration? These bad boys lock tight.
Manufacturing Processes for Carbon Fiber Connectors
Building connectors for carbon fiber tubes isn’t just about slapping pieces together. It starts with prep. Choose quality carbon fiber tube cloth or pre-preg sheets. Lay it into a mold or wrap it around a mandrel. Add resin. Then heat-cure or vacuum-bag depending on the method.
Small-batch builders often use hand layup with carbon fiber tube making machines. Those chasing perfection go for filament winding. That method gives consistent strength, ideal for tight tolerances and carbon fiber tube compression strength testing.
Want connectors made faster? Try 3D printing molds. Pour resin composites. Clamp. Cure. Done.
Advantages of Carbon Fiber Connectors
Why bother using carbon fiber connectors at all?
They weigh less than aluminum yet pack serious strength. Corrosion? Nope. Not here. Carbon fiber tube strength tests blow past expectations. Add connectors made from the same material and you’ve got a featherweight beast ready for stress.
Another perk? Vibration damping. Quad flyers know the struggle. Too much shake, and the drone crashes. But add the right connector between carbon fiber tube arms, and flight becomes smoother.
They also don’t deform like plastic under heat. Need a part to hold up inside your telescope mount or survive desert races? You’re covered.

Choosing the Right Connector for Your Project
What works for carbon fiber tubes for kites won’t cut it for a 100mm telescope frame. Choosing wrong causes headaches—loose fits, stress cracks, wasted time.
Ask these:
Is the joint permanent or adjustable?
What’s the expected load?
How many cycles of use?
What tube diameter? (carbon fiber tube 100mm or micro-scale?)
Will it face compression or bending?
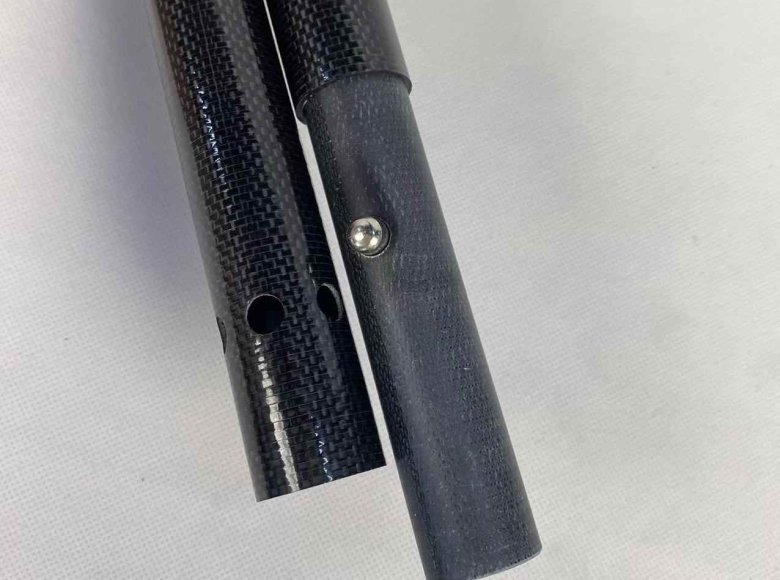
Bonus Tips for Better Results
Don’t force fits – Tight connectors can stress the fibers. Sand or shim as needed.
Use epoxy with care – Good bond, bad mess if overdone.
Clamp well during cure – Misalignment means failed builds.
Test first – Compression? Bending? Run a carbon fiber tube test before scaling up.
Protect edges – Use carbon fiber tube protector rings to avoid splintering.
Building telescope frames? Quadcopter arms? Or maybe something wild like carbon fiber tubes for kites? Always plan your assembly steps. Cut clean. Align true.
Want simple? Grab a carbon fiber tube cutter from eBay and chop to fit your length. Then pair with clamp-style connectors from carbon fiber tube suppliers—many ship worldwide, including carbon fiber tube South Africa warehouses.
Working on prototypes? Avoid complex molds. Use sleeves or printed inserts instead. They’re easier to test and replace.
Wrap-Up
Simple doesn’t mean sloppy. Even a basic carbon fiber tube fabrication project needs thought and solid connections. Use the right connectors, prep your parts well, and test before locking anything in place.
Carbon fiber tube bending may sound tricky—but connectors remove the need for curves altogether. Straight lines, sharp fits, cleaner builds.
Want to go deeper? Find a good carbon fiber tube manufacturing partner. Whether you’re sourcing parts from Los Angeles or hunting for a supplier across the pond, start with the right gear. Then let your project fly.
References:
1. How To Cut Carbon Fiber Tubes: Key to Tolerance and Customer Relationships
2.How We Helped Our Client Solve Product Issues with Our Carbon Fiber Tubes?
3.Can Carbon Fiber Tubes Be Mass-Produced? Here’s What You Need to Know
4.How to Improve the Surface Quality of Large Diameter Carbon Fiber Tubes
5.Why Is the Carbon Fiber Tube 50mm OD 47mm ID So Popular?
One Response